投料
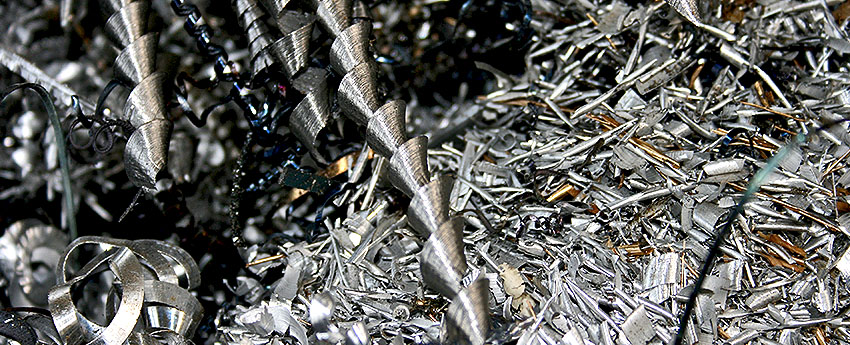
Welding, grinding, laser and plasma cutting, spray painting and powder coating of metals generate potentially dangerous fumes and particulate matter that require dedicated ventilation / filtration systems to ensure a safe work environment.
Welding Fumes & Particulate Matter
Welding involves the melting and fusing of workpieces together with a molten filler material and possibly shielding gases. The process can be dangerous and unhealthy if proper precautions are not taken. New techniques and appropriate protection however do offer the means to reduce the risk of injury and death.
Hazards
Among the various hazards, welding fumes and particulate matter represent potential dangers that face operators. OSHA highlights zinc, cadmium, beryllium and iron oxide as possible elements that may be released to the ambient air depending on the metals welded. Exposure to such airborne contaminants should be confined to designated areas and welders provided proper personal protection, ventilation and training.
Each Welding Method Has Their Pros And Cons That Need To Be Addressed:
Robotic welding uses mechanized programmable tools (robots), which completely automate a welding process by both performing the weld and handling the part. This method generates a considerable quantity of fumes and sparks.
Shielded metal arc welding (SMAW), manual metal arc welding (MMA or MMAW), or simply "stick welding" produces smoke and often requires a self-cleaning fume extractor to avoid filter obstruction.
Gas metal arc welding (GMAW), commonly termed MIG (metal, inert gas) or metal, active gas (MAG) welding produces smoke containing particles of various types of oxides. The size of the particles influences the toxicity of the fumes, with the smaller particles representing a greater danger.
Gas tungsten arc welding (GTAW), also known as tungsten inert gas (TIG) welding generates little, if any smoke.
Each welding method and material type must be assessed to ensure appropriate filtration media are chosen. Here are some examples:
- HEPA filters are well suited for stainless steel welding.
- Nanofiber filters meet the needs for welding aluminum and parts containing high levels of manganese.
- Polyester filters are satisfactory where rust inhibitors, lubricants and coatings may generate an oily smoke.
Grinding and Deburring
Grinding and deburring activities generate airborne particulate matter that should be confined or removed from the operator’s working environment.
Typical sources include grinding, angle grinders, die grinders, automated grinding machines, deburring stations and many other abrasive processes.
Hazards
Grinding generates significant quantities of dust and sparks which require a large number of filtration media to handle the increased loading. Deburring produces submicron particles that can only be filtered with units that qualify as HEPA.
Laser & Plasma Cutting
The two main thermal cutting processes employed in industry to cut steel, metals, plastics and sometimes other materials are laser and plasma cutting.
Laser cutting
Used in serial manufacturing by directing a high-power laser light beam, with the help of laser optics and CNC (computer numerical control) to cut flat-sheet and structural steel or metal alloy components.
Operation / efficiency
The metal melts, burns, or vaporizes away by a jet of gas, leaving a remarkably clean edge with little, if any, asperities. Although principally used to cut metal, various plastics are also cut, engraved and etched with a laser. Cutting acrylic is common, but other types of plastics may be cut with a laser, such as polycarbonate, polypropylene and polyethylene.
Plasma cutting
Utilizes a gas, such as nitrogen, argon or oxygen, which is projected at high velocity through a channel / nozzle in combination with an electric arc to produce a plasma torch.
Operation / efficiency
The extremely high temperature of the plasma stream melts and projects the molten metal and slag away from the shear surface. Secondary channels on the nozzle periphery allow the constant flow of shielding gas to control the radius of the plasma beam and protect the cut from oxidation. As with other robotized equipment, CNC technology applied to plasma cutting devices provide the needed flexibility to cut a myriad of patterns, shapes and sizes with accurate cuts, leaving no metal chips. Recent technological developments allow smaller nozzles with narrow CNC plasma streams which boast near-laser precision on plasma cut edges that surprisingly require little or no finishing.
Additional Information
Hazards
Despite their unmistakable advantage in the mass production of finely cut, seemingly tailor-made manufactured parts, these technologies represent a potential threat to worker health and safety.
The IRSST (Quebec), NIOSH (USA) and research affiliates in England, France and Germany provide concerted guidance to promote worker health and safety in industry.
Laser and plasma cutting of metal creates metal dust, smoke and fumes that are unhealthful to breath. OSHA recognizes zinc, lead, beryllium, cadmium, manganese, nickel and chromium as possible hazardous elements that are released to the ambient air depending on the type of metal cut.
Coated metals
Some metals are coated, such as galvanized steel, lead or cadmium-plated steel: We recommend you remove the coating from the cutting area if possible. These coatings and any metal containing these elements give off toxic fumes when cut with a plasma arc. Of particular concern is hexavalent chromium, a coating used in metal finishing to prevent corrosion on stainless steel and other metals: plasma torch cutting of this material exposes workers to hex chrome dust, which is a heavy metal known to be a potent carcinogen when inhaled. In 2006, OSHA enforced regulatory compliance to protect employees from hexavalent chromium exposure.
Laser cutting of plastics
Laser cutting of plastics such as polypropylene, polyethylene and polycarbonate generates benzene, a carcinogen. Polystyrene gives off styrene, while PVC releases hydrogen chloride. Many plastics release submicron particles, in addition to carcinogenic PAHs (polycyclic aromatic hydrocarbons). Fluoropolymers such as PVDF, ECTFE, PFA, FEP and PTFE (used as a non-stick coating for hot plates) are sensitive and start to react at moderately high temperatures, giving off hazardous fumes.
For these reasons, we recommend capturing fumes at their source. If this is impractical, down-draft containment of rising fugitive gas emissions that escape the immediate vicinity of thermal cutting tables may be an acceptable compromise. And if these methods do not suffice, it may be necessary to design complete systems that include ventilation of open areas and thus encompass all avenues of fume propagation.
To Summarize
First and foremost
Capture the thermally generated fumes at their source. Plasma and other thermal cutting generate sparks, slag and fumes that contain different contaminants depending on the type of material cut. These heavy smoke applications require high capture velocities at source to avoid contamination of the work environment outside the enclosure.
Secondly
Down-draft containment limits propagation by encapsulating fumes that migrate to the backside and/or underneath cutting tables. Keep floating sparks at bay and avoid their dispersion upward as these may blend inconspicuously with rising smoke; uncontrolled and unmonitored, these mixtures constitute a serious fire hazard should they enter the dust collection system.
Finally
To assess available techniques that will effectively capture and filter fumes generated from large CNC plasma cutting and laser cutting machines, it may become apparent that only a large central dust collector is suited to pneumatically convey the intense smoke and vaporized metal / plastic dust in a safe and secure manner. AIREX provides an inline spark arrestor / suppression conduit along with a self-cleaning dust collector with multiple filter cartridges as a possible comprehensive solution to remove airborne contaminants from thermal cutting operations.